Online reading
Mark Rosenthal’s blog is always great. I recommend his recent post called “Boeing: The Turning Point(s).” He connects Boeing’s ongoing difficulties to two attempts to change company strategy twenty years ago. I enjoyed Mark’s detailed reminiscences from the time:
There were actually two lines running parallel, each one on a two day cycle. … Each time the line was indexed, it generally took a shift to, in succession, pull each plane back, then forward, then dock it into the next position. And because this was a schedule-driven line, the planes moved on time, ready or not. Incomplete work became “travelers”—jobs that traveled with the plane to be completed later when, for example, the parts became available. Exactly who was supposed to do that out-of-sequence work while everyone was busy with the scheduled jobs was a little vague.
The assembly manager for 737 then ran an experiment. Instead of trying to solve all of the problems they could think of before trying anything she took the opposite approach. She got an RV winch, bolted it to the floor by the door, hooked the cable to the last plane, and started pulling it—slowly—through the work position.
If everything was going smoothly, they kept pulling. If something disrupted the work, they stopped the winch, wrote that down, and picked off a few of those things to try to fix on the next cycle.

Daniel Katz writes that, even though we add new people to groups in order to address medium- or long-term needs, there are also short-term benefits:
The act of adding a new person also has immediate benefits to the group, as a new person who doesn’t know the practices and culture of the group can reflect on them as they learn them, ideally leading to lessons and improvements for the whole group.
I think about this often as a consultant—e.g. a person sometimes inserted into groups on a temporary basis, and who sometimes pushes the dirt around when organizations expand, split, or rearrange.
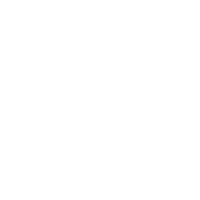
And Michel Baudin assembled a long, informal survey of different attempts to define “quality” in operations & management contexts. The theme is that people love to talk about quality, but no expert knows, and no group agrees about, what it is:
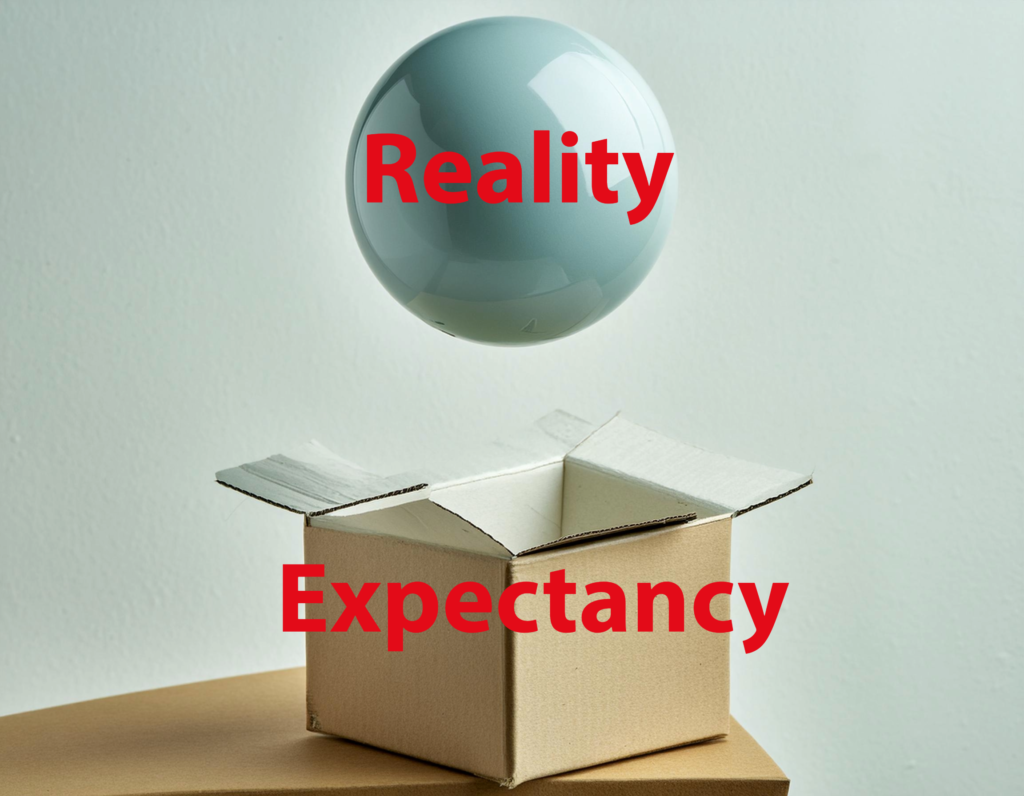
This all becomes a problem in lean interventions—as transmitted by Lean Enterprise Institute, et al—which begin by spinning a group’s tires in an intractable, wasteful effort to produce a working definition of “customer value,” of which “quality” is one component. Of course, none of this is necessary and is best avoided. But the waste and confusion these conversations produce is one reason I walked away from those methods and found better ways to spend the time.
Baudin’s piece brought to mind this entertaining, possibly apocryphal, quote from designer Massimo Vignelli. It bears the confidence of someone who (a) knows quality when they see it, (b) does not care to explain, and (c) will be submitting an invoice:
There are no hierarchies when it comes to quality. Quality is there or is not there, and if is not there we have lost our time.
Disability Pride Month
July is Disability Pride Month, which commemorates the 1990 passage of a key civil rights law in the USA—the Americans with Disabilities Act (ADA).
I wrote on this topic last year:
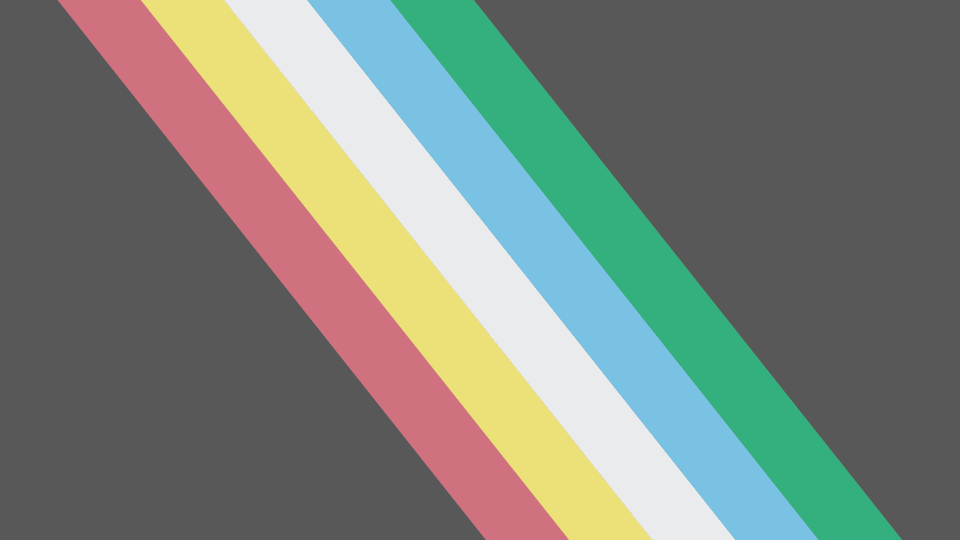
Two points I’d add this time around:
- The experience of disability has entered my family life in a different, terrifying way in 2024. I am grateful for the limited protections and affordances of the ADA that helped us these past months.
- Many of those same protections are now at risk as a result of one of June’s disastrous set of US Supreme Court decisions.
Why discuss any of this at all? Because my disability has mostly been a “hidden” one, and at some point I became tired and ashamed of all the work that went into keeping it so. My disability is an important part of who I am, and—as I wrote in the piece—I have a good life and I do good work.
And that’s it for the moment. Be back next month with more links & notes, and hopefully some other updates in-between.