2023 is the year of economic headwinds, of the “soft macro,” and the return of an old, wet noodle of a rallying cry:
“We have to do more with less!”
This cliché keeps coming around. I first heard it at my first job after college, where it was issued as a resource for bravery, an utterance that utterly backfired. In the decades since, I keep hearing it.
Each time, something about the phrase makes me want to fill in the blanks—“Do more (of what?) with less (of what?).”
As far as I can tell, the general usage seems to be:
- Doing more of this → Making money for the company
- With less of this → People
OK, that sucks! But first, wanna know where the slogan came from?
Bucky Fuller’s “ephemeralization”
Back in the 1930s, Fuller coined ephemeralization—which he defined as the capability of technological advancement to do “more and more with less and less until eventually you can do everything with nothing.”
Here it is, on page 279 of Fuller’s Nine Chains to the Moon (1938):
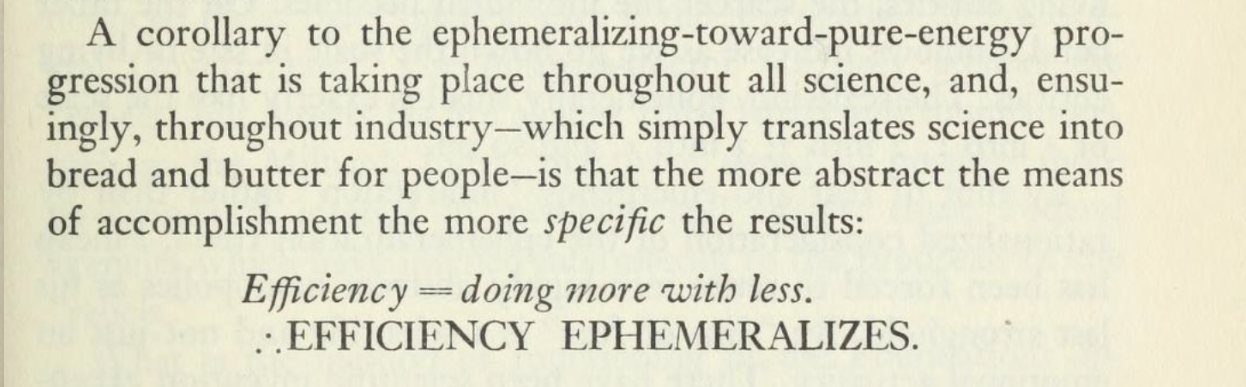
If you are not fluent in Fullerese, please skip hundreds of pages of turgid reading and know that in his framework “doing more with less” entailed:
- Doing more of these things → Curing disease; eliminating infant mortality; providing housing and food for every family on Earth; and increasing the standard of living—and the freedom available for science, for art, for play, for leisure—with no upper limit
- With less of these things → Time, space, and energy
What I wonder is… how’d we get from all that—from the translation of “science into bread and butter for people”—to the current jargon, where it means nothing other than “do the work of five people but with 3, even though our company already sheds cash like a housecat made out of money.”
In the 2023 “soft macro” condition of “doing more with less,” the mechanism by which people are meant to actually accomplish this lessening is deliberately undefined. It’s the same old management-by-objective horseshit: “more with less,” but with no material or managerial support, an effort totally unlinked from the value chain.
From five to three—but what of the two?
In lean management, there’s an answer for what to do when people come up with improvements—even improvements so effective that they take the work of 5 people and turn it into the work of three. There has to be an answer, because as soon as an organization starts a serious practice of continuous improvement, it will find improvements like that. Always. Opportunities are just lying around, and the methods will uncover them.
Anyways, the lean management answer is this: OK, three people will now do that work previously done by 5, in a way that is safer, faster, more reliable. This frees up the remaining two to go do something else within the organization. Maybe it’s helping another group get ahead, or helping peers learn continuous improvement. Maybe it’s starting a new project. Nobody loses their job. Nobody is catapulted to the next stage of their career via layoff. And all this gets accomplished in a way that everybody can see the changes in quality, cost, and safety.
It’s critical that management believe in this answer, communicate it effectively, and stick to it over time.
Why? Because that’s what moves an organization:
- from the (bad) condition where people worry about working themselves out of a job, or observe that they will be punished and/or ignored for noticing problems at the workplace…
- to the (good) condition where people become deeply engaged in noticing problems and designing improvements to their own work.
It may not be Bucky’s Utopian, humanist vision of translating “science into bread and butter for people,” but it does mean helping people get the work done on time, with less hassle, and respecting the wisdom and capabilities of everybody involved. And… at least for now, you know, I’ll take it.